Web Inspection Solutions to Tissue Mills
Procemex Web Inspection System for tissue covers your quality and efficiency improvement needs on your tissue machine and converting line. It also makes it safer for operators to monitor key locations of the machines. Key elements for problem solving and troubleshooting on a tissue machine are Web Inspection and Web Monitoring systems. The paper defect and web break root cause information captured is used to reduce the number of web breaks and control product quality. In addition to that, the critical data is transferred with reel defect maps into converting lines to enable smart decisions supporting higher converting line runnability.
Procemex develops and manufactures their own Matrix Smart Camera and LED lights specifically for the pulp, paper and tissue industry.
Powerful LED Strobe Lighting
- Smart Camera pulses LED strobe only during image exposure; reducing heat generation due to decreased illumination time which significantly extends the life of the LED lighting
- Strobing provides powerful illumination peak to stop the web movement, eliminate blur and produce photographic image quality
- Any LED segment can be changed at any time without creating a degradation in detection performance and the overall capabilities of the system
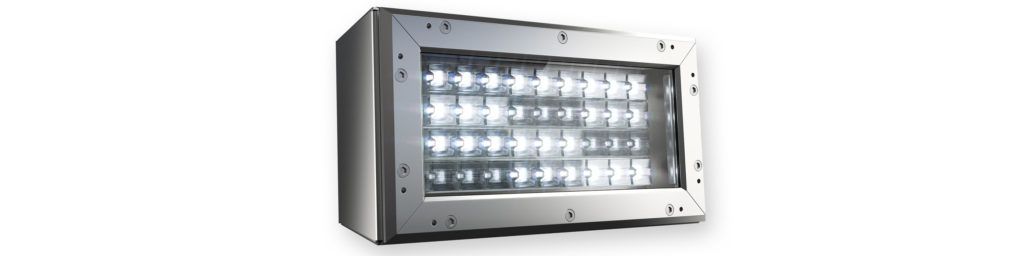
HD Pinhole Cleaning Concept
Web Inspection is typically located at the end of tissue machine in dusty environment. Unique patented pinhole camera beam or separate pinhole camera housing keep cameras clean.

Different Detection Geometries
The Smart Camera can make several independent measurements by pulsing different LED light profiles to flash
sequentially for alternating inspection.
Utilizing Procemex carbon fiber beams guarantees evenness of illumination and a long-term alignment of cameras and lights. In case there is not enough space or if a lower price option is preferred, it is also possible to use separate
cameras and lights for the same purpose. This leads to more uneven illumination and extra maintenance/alignment work on cameras and lights is necessary over the lifetime of the system.
Transmission Web Inspection


High Angle Reflection Web Inspection

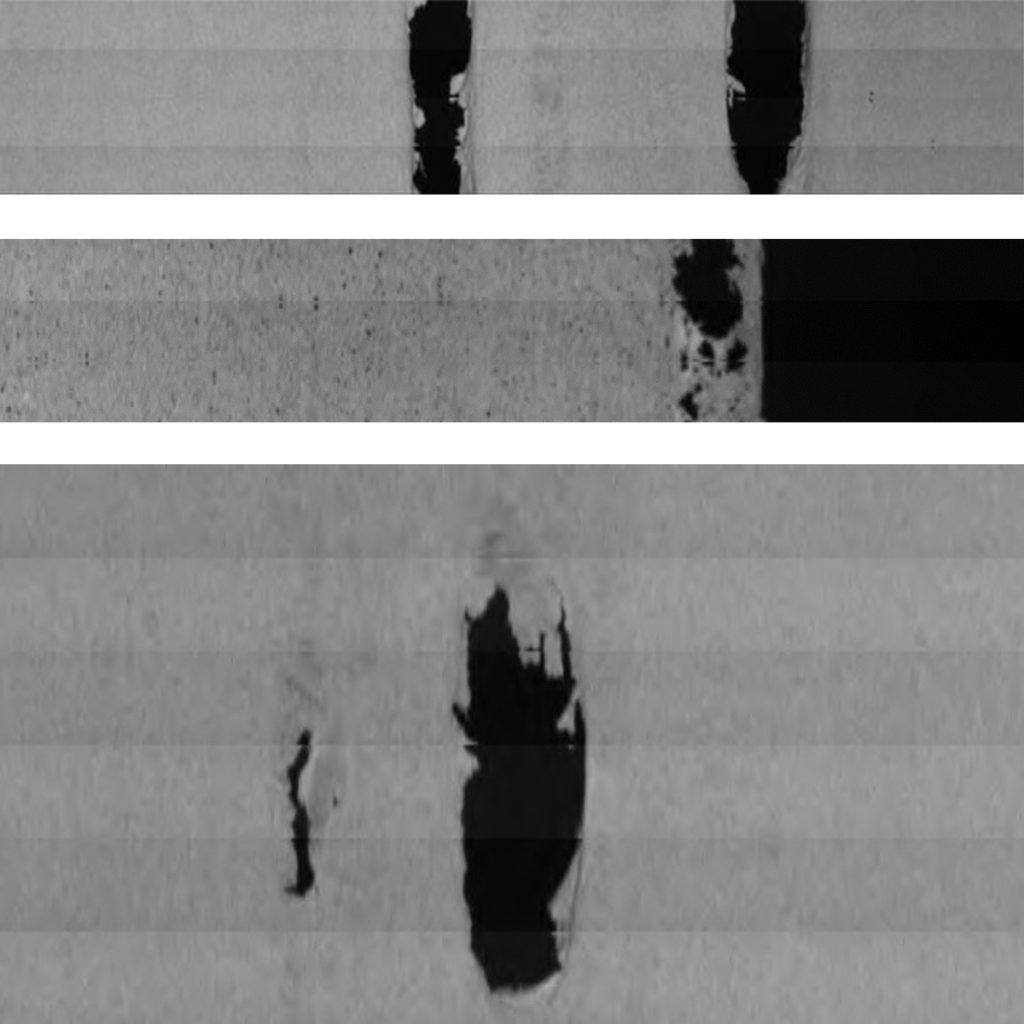
Alternating Light Web Inspection

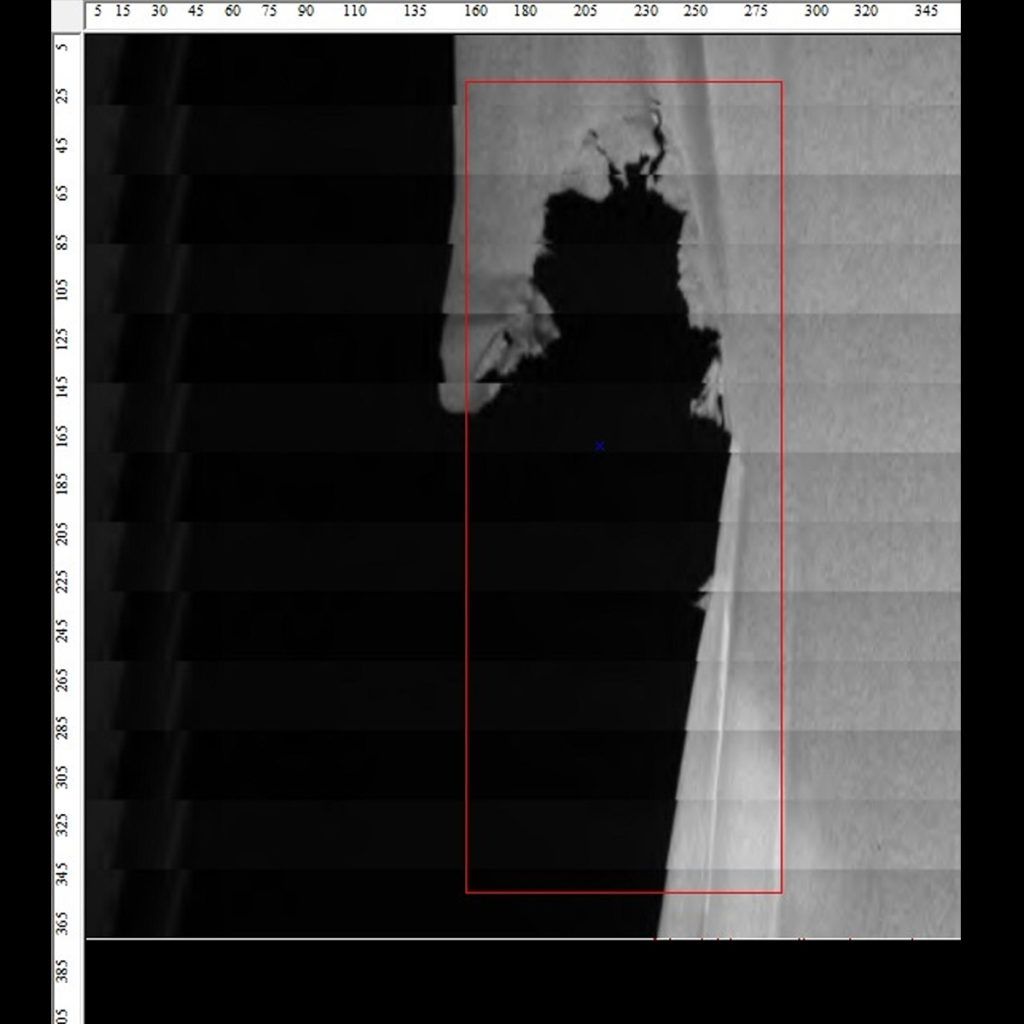
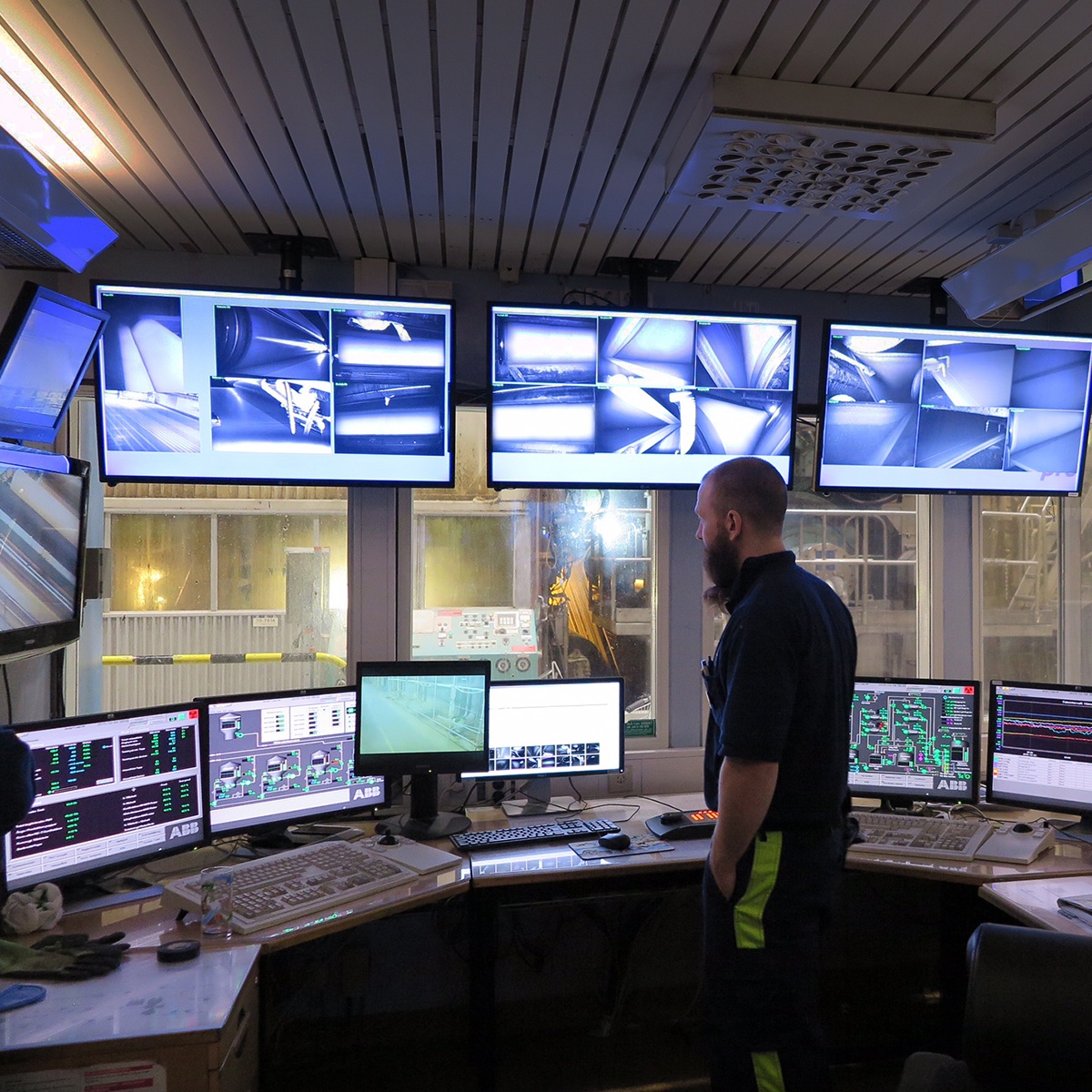
Classification
- Matrix camera imaging provides higher quality images to the classification engine and increases accuracy over antiquated line-scan technology
- Procemex utilizes a floating defect filter to reliable separate defects in the sheet from floating dust and debris in the area
- Smart Camera enables direct pre-classification in the camera and real-time outputs are available for external use
- Post-classification beyond single inspection frame measurement utilizing all data available for the most accurate classification
- Advanced Classification utilizing the VisionAppster Platform for developing and acquiring tailored traditional and neural network classification algorithms
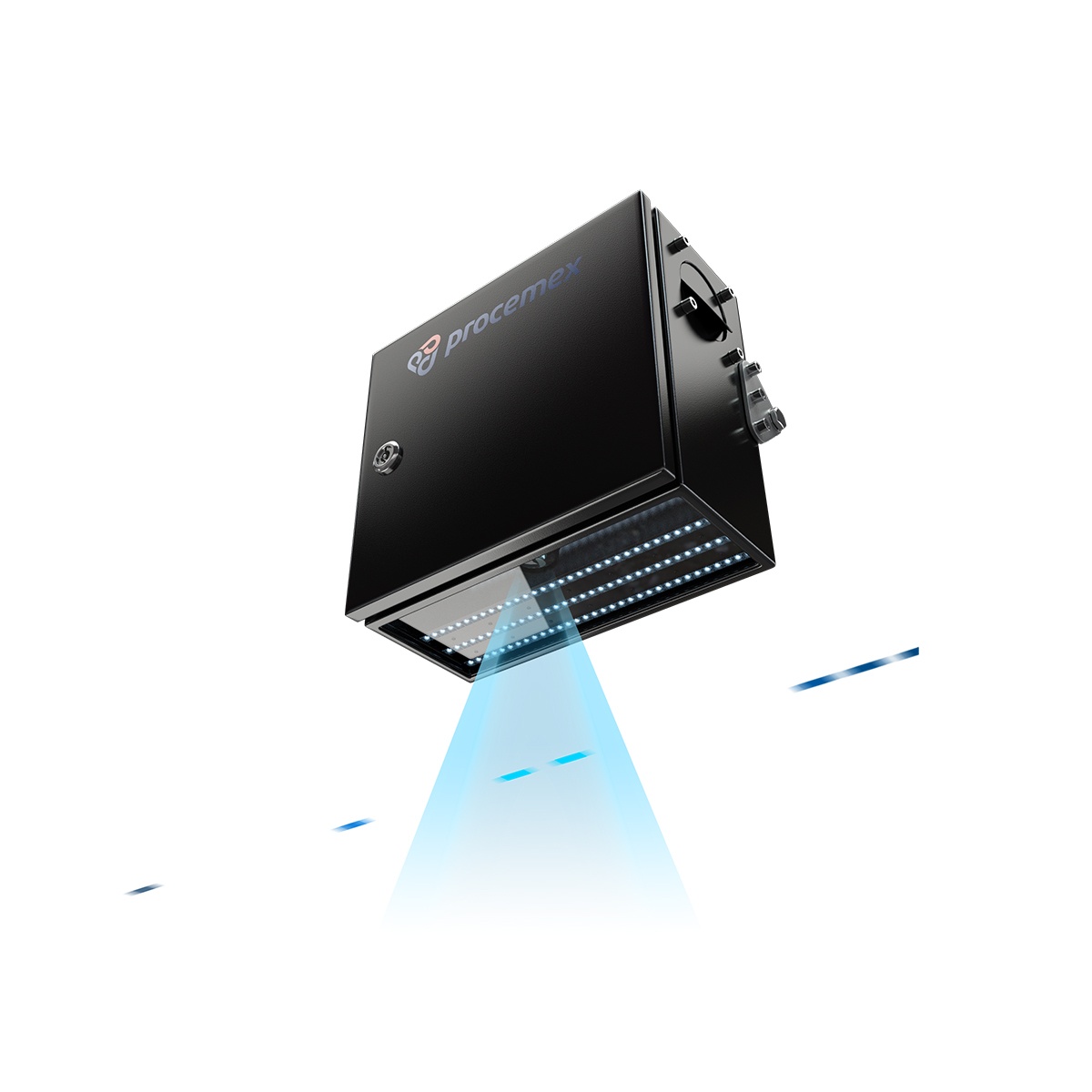
Automatic Target Control | ATC
A marker located at the end of the tissue machine puts an ink code with the MD position information on the edge of the sheet. A reader on the winder reads the code and synchronizes the defect map with the actual current position and enables an automatic stop or crawl function to react on customer defined defects.
- Automatic reel and defect map loading
- Customer roll set position can be overlaid
- Selected slow down or stop targets indicated on defect map