Automatic Threading Rope Monitoring
The Automatic Threading Rope Monitoring examines the condition of threading ropes and their expected lifetime 24/7. The Automatic rope condition monitoring prevents serious damages and expensive unplanned production shutdowns.
Significant cost savings
- Broken threading ropes cause expensive paper machine down time
- Installing a new rope requires shutting down the paper machine
- Threading a new rope through the machine without the old rope can take 12 to 24 hours depending on the damages
- Annual total cost caused by rope breaks can be > 0,5 M €
- Automatic Threading Rope Monitoring enables rope changes as preventive maintenance during scheduled down time
- Rope breaks are a safety hazard. They can cause severe damage to people and equipment.
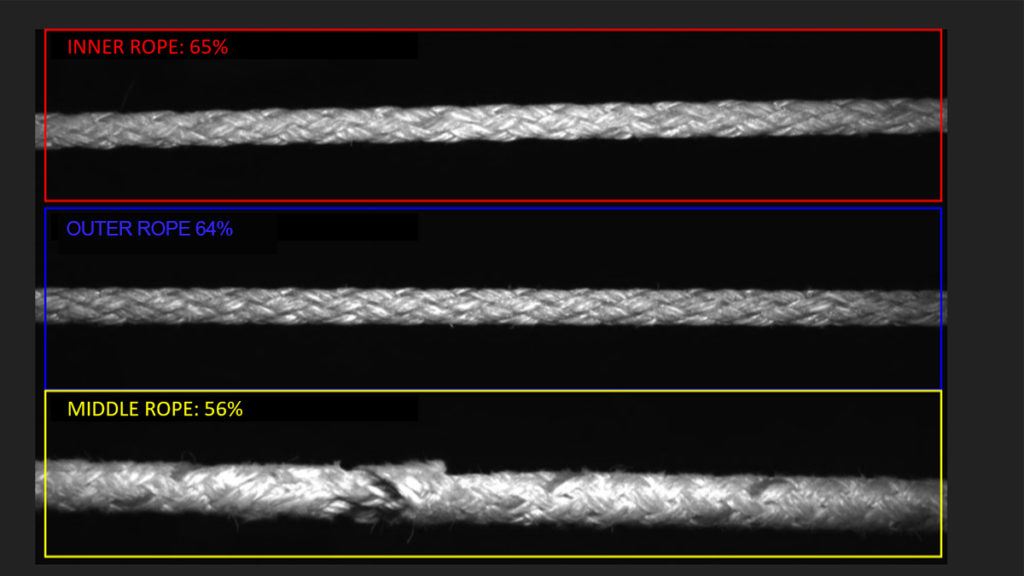
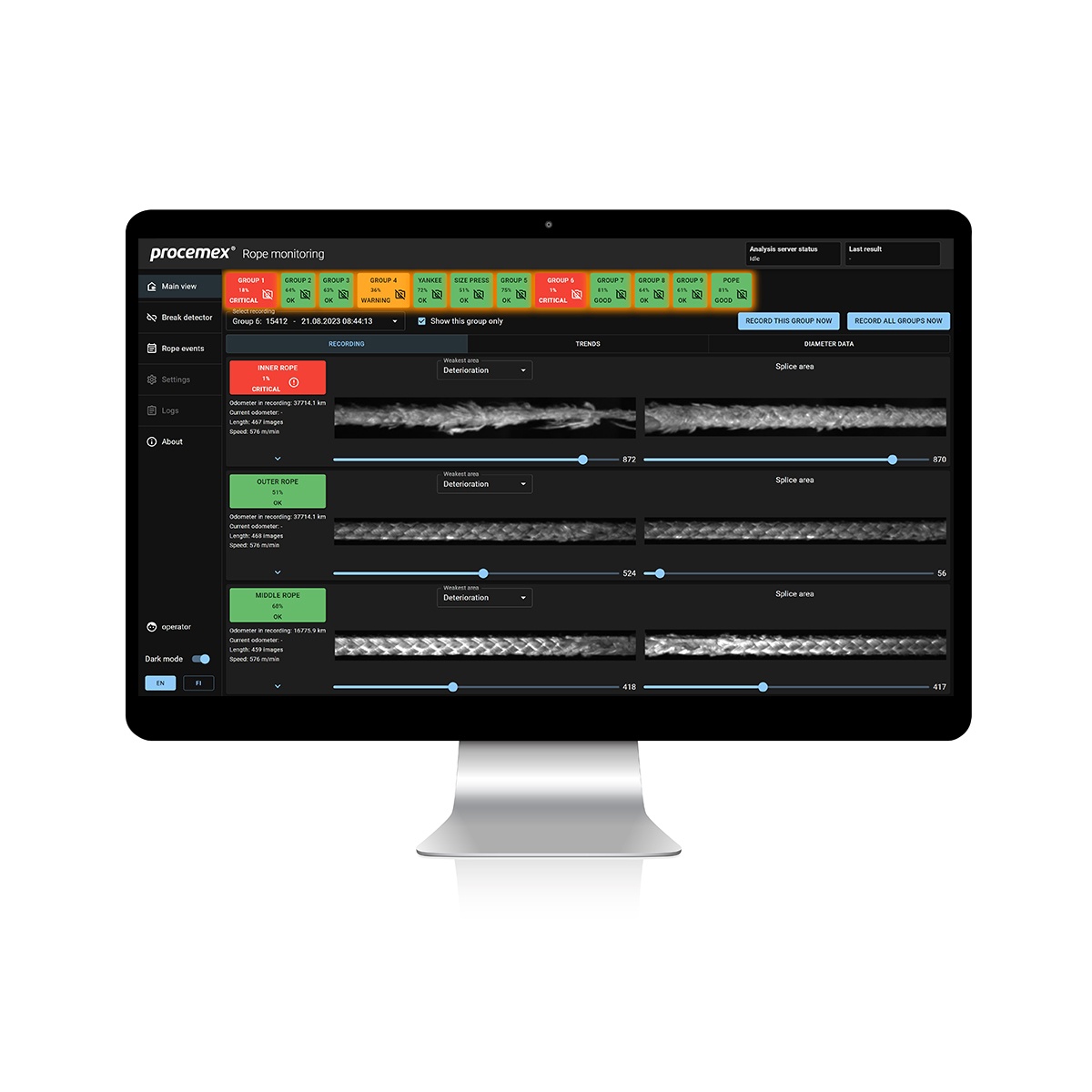
Rope Condition Monitored 24/7
- Monitors threading rope’s condition and expected lifetime 24/7
- Increases the mill safety
- Helps to prevent:
- Unexpected rope & web breaks
- Unplanned machine shutdowns
- Optimizes threading rope change intervals
- Saves operators’ time
Success Stories
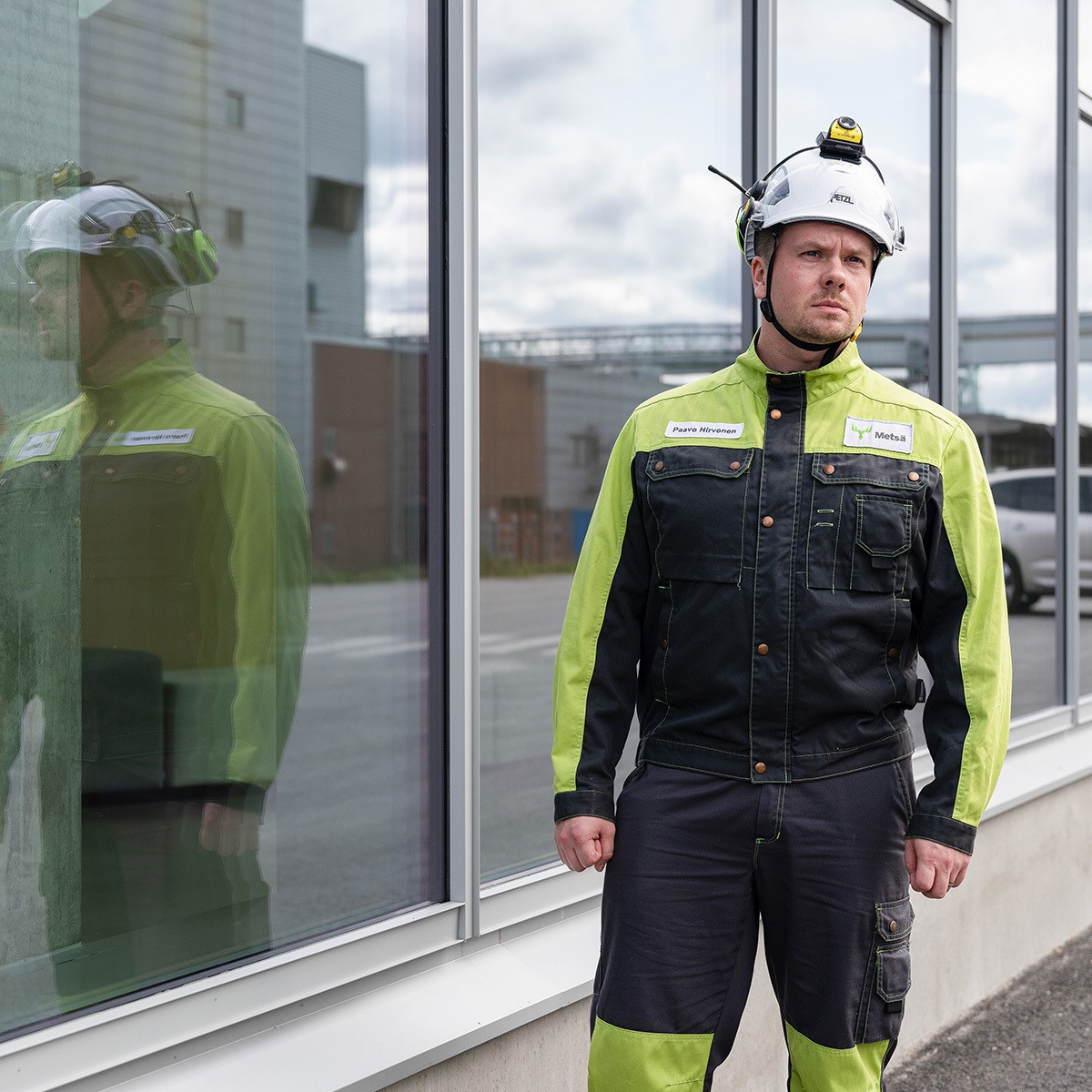
Success story
Metsä Board Äänekoski, Finland monitors Carrier Rope Condition 24/7
The latest functionality adopted by Metsä Board Äänekoski, Finald has been the Tail Threading Rope Condition Monitoring. The carrier ropes’ condition is continuously monitored with Procemex cameras utilizing cutting-edge AI-analysis technology. As a result, the threading rope changes can be conducted as preventive maintenance during scheduled machine shutdowns, reducing the number of unexpected and expensive web breaks and machine down times.
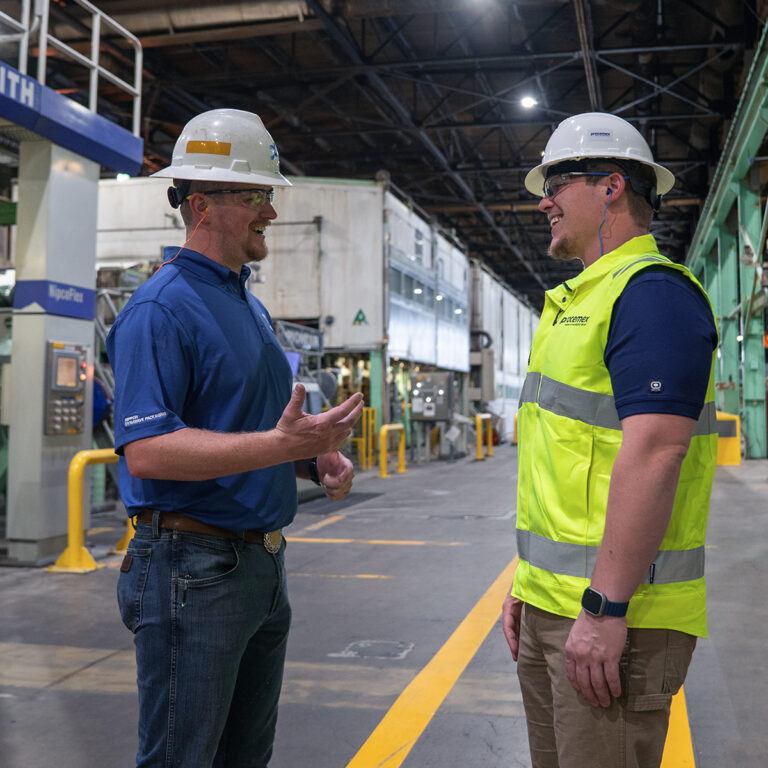
Nippon Dynawave Packaging: Superior Product Quality and Increased Uptime with Procemex Web Monitoring and Web Inspection System
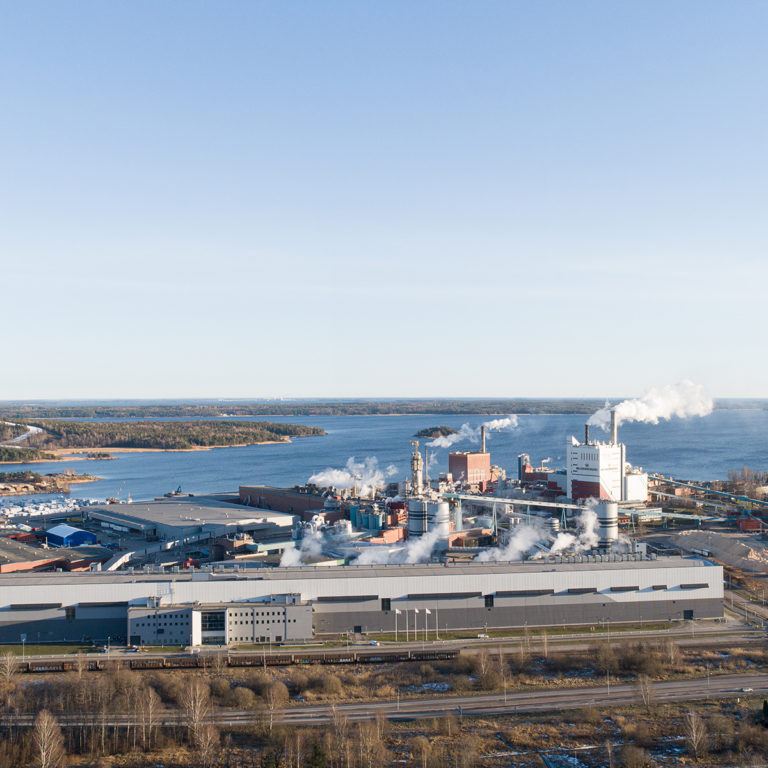
BillerudKorsnäs Gruvön Mill: “We Are Really Happy to Run Procemex OnePlatform System”
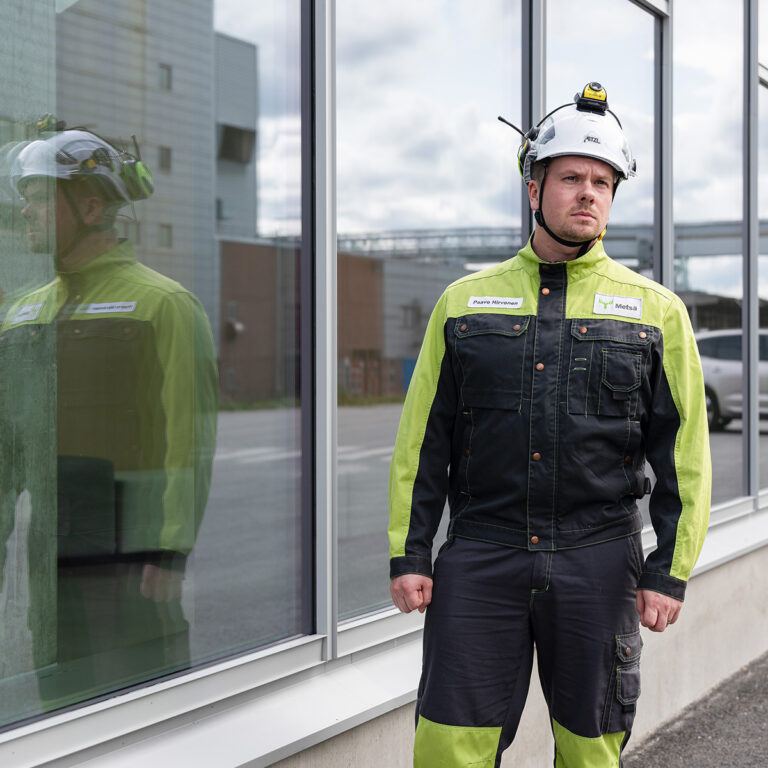
Metsä Board Äänekoski: Higher Customer Satisfaction and Line Efficiency with Procemex Web Monitoring and Inspection System
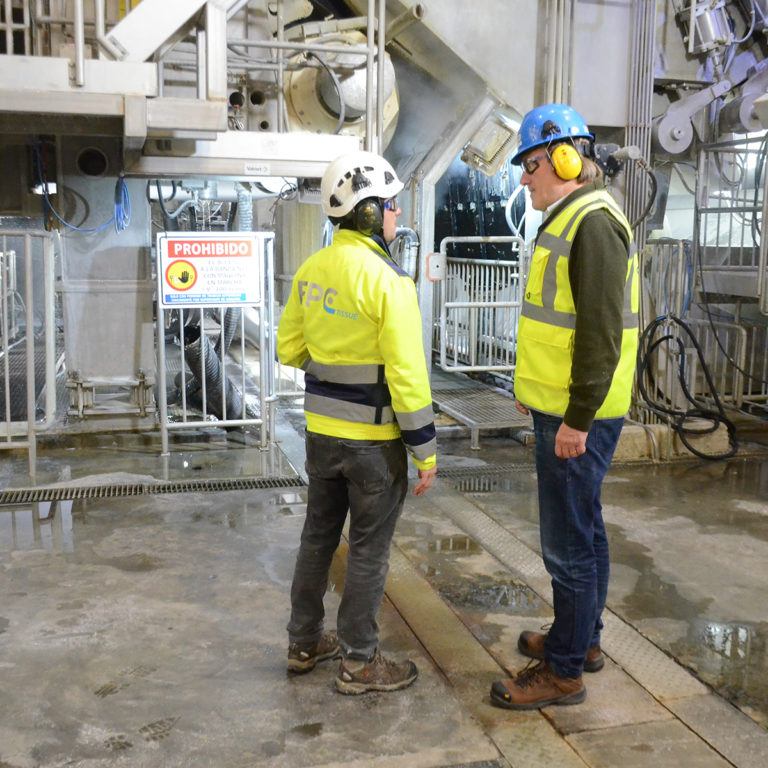