In the pursuit of achieving supreme customer quality requirements, Metsä Board Äänekoski found itself at a crossroads. The need to enhance the Web Inspection and Monitoring capabilities had become vital, driven by the solid commitment to excellence. After thorough research and planning, the path ahead became apparent, and Metsä Board Äänekoski embarked on a transformative journey with Procemex.
Striving to meet the increased customer quality requirements
The biggest drivers for Metsä Board Äänekoski to make the significant investment were two-fold. Firstly, the increasing customer quality requirements underscored the need for a new vision system to better meet current and future customer needs. Secondly, the old system had come to the end of its lifespan and there was a need to enhance defect detection capabilities and analyze the root causes for web breaks more efficiently. “We sought a solution that would allow us to see defects with improved accuracy and precision, surpassing the capabilities of our previous system. When assessed through various metrics, Procemex’s solution emerged as the one with the most compelling value proposition,” says Environmental Manager of Metsä Board Äänekoski Paavo Hirvonen, who was the project manager for this development project.
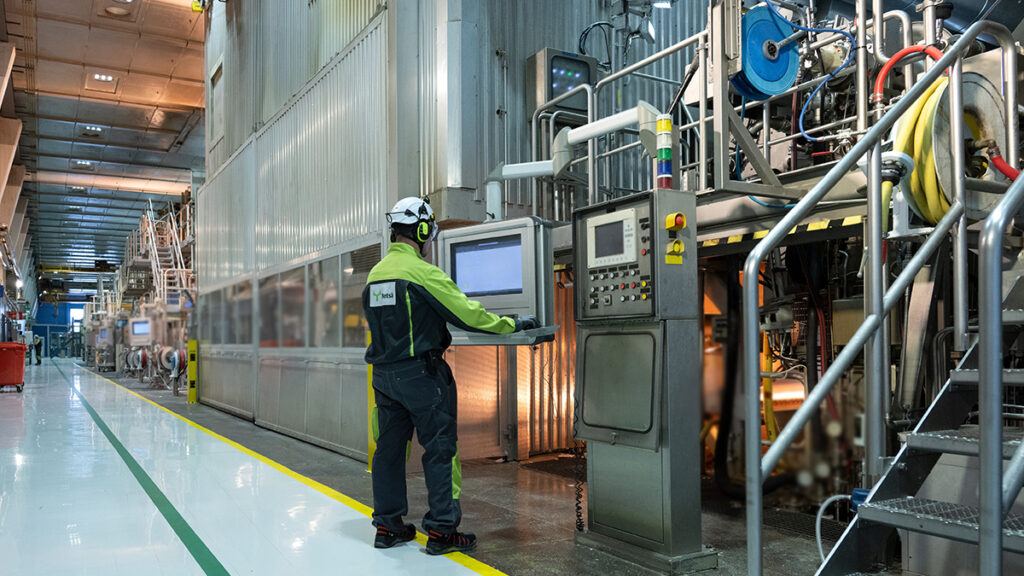
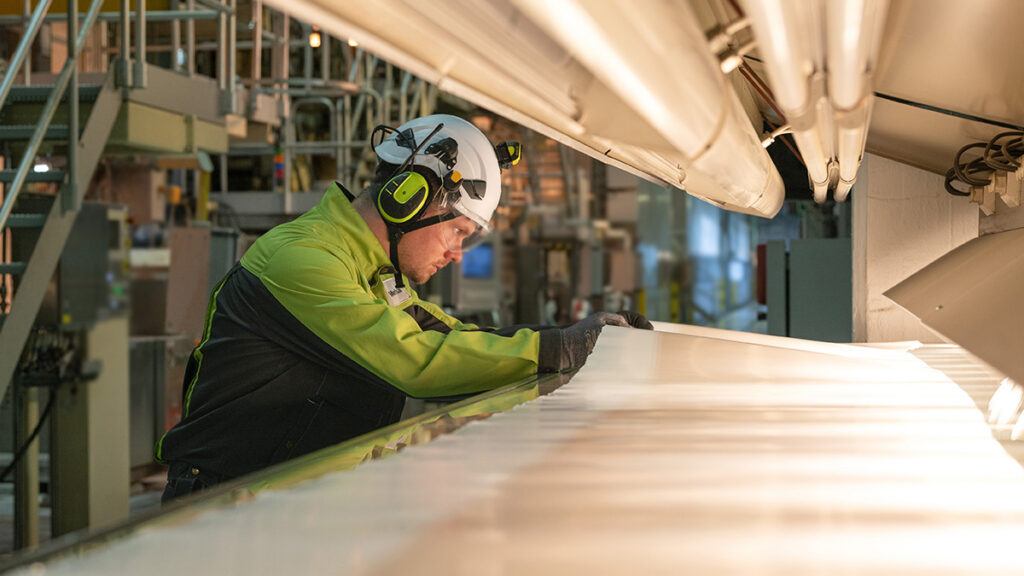
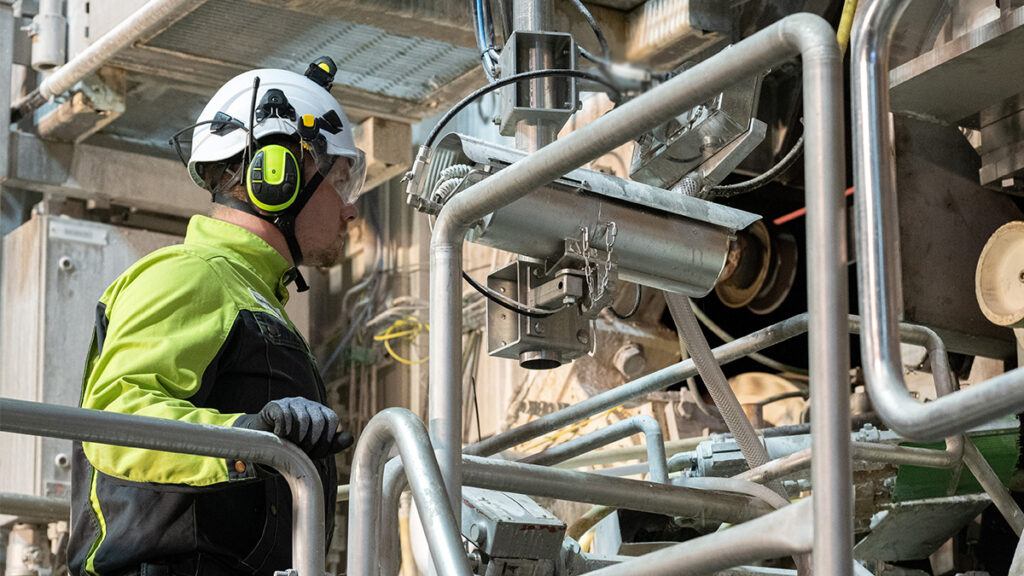
Decision drivers
The decision to partner with Procemex was fortified by several factors that linked seamlessly with Metsä Board’s vision for excellence.
Before deciding, Metsä Board Äänekoski carefully investigated references from varied sources within the Metsä Group and industry. The positive experiences shared by others who had partnered with Procemex instilled a sense of confidence for Metsä Board Äänekoski that they were aligning themselves with a proven leader in the paper Web Inspection and Defect Monitoring field.
Additionally, Metsä Board Äänekoski valued the expertise of Procemex’s technology development and service team. “One of the most important reasons that drew us to Procemex was their commitment to in-house camera technology development. Their ability to harness cutting-edge innovation within their own walls resonated deeply with our quest for future-proof pioneering solutions that set us apart from our competitors,” says Paavo Hirvonen. Furthermore, virtualization and integration into Metsä Board Äänekoski’s ICT infrastructure was one of the selection criteria. The assurance of having 24/7 system support added an extra layer of confidence to the decisionmaking process within Metsä Board Äänekoski’s project team.
Enhanced defect detection and root cause traceability
There was a great need to detect defects quickly and precisely to meet the increased quality needs of customers. The folding boxboard is inspected at two distinct locations at the reel. Positioned steadily in mechanically stable carbon fiber Web Inspection frame, the cameras detect and classify coated product surface defects at 0,10 mm pixel resolution.
“With the new camera technology, we can see coating blade streaks and other defects better than before”
Paavo Hirvonen
The low-angle inspection geometry uses a 15 degree camera angle and a 15 degree illumination angle to provide a mirror reflection from the folding boxboard surface. This enables the detection of very small coating defects, such as streaks or coating skips.
The transmission detection is used together with the high-angle reflection detection. This unique twoprofile measurement geometry with sequential illumination is used for detecting and classifying surface defects as well as defects inside the product. It provides a foundation for more advanced and reliable defect classification and root cause analysis.
In addition to Web Inspection, there are almost 60 smart cameras monitoring Metsä Board BM1’s product quality and production efficiency.
Strategically positioned Procemex ProClean Pinhole cameras monitor the board machine landscape, unveiling the root causes of web breaks and product defects.
“The fully integrated Web Inspection and Monitoring System has been a game-changing tool for us to find the root causes of web breaks and improve production quality. Furthermore, the new cameras stay cleaner and provide much better image quality compared to our previous system, which converts into better efficiency”
Paavo Hirvonen
The latest functionality adopted has been the Tail Threading Rope Condition Monitoring. The condition of the carrier ropes’ is carefully monitored 24/7 with cameras utilizing cutting-edge AI-analysis technology. As a result, the threading rope changes can be conducted as preventive maintenance during scheduled machine shutdowns, reducing the number of unexpected and expensive web breaks and machine downtimes.
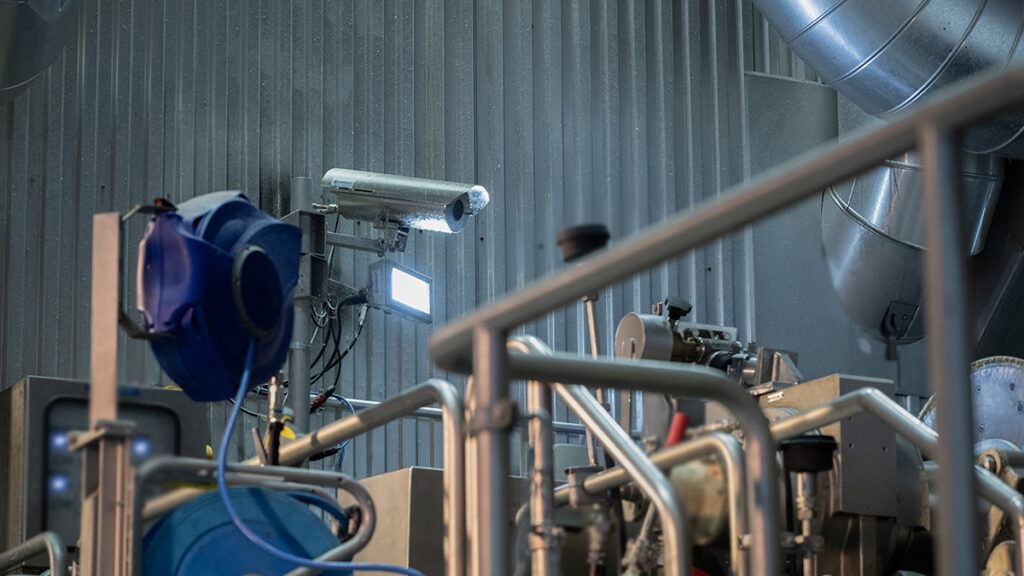
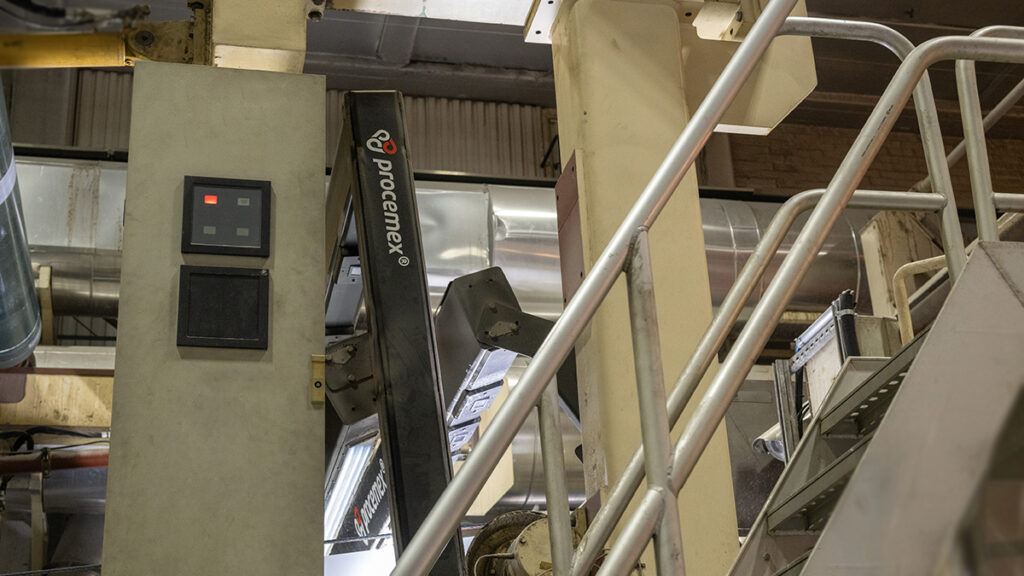
A skilled service partner to ensure smooth system operation
Procemex is known globally for its skilled service operations, where a local team of professionals rapidly responds to customer requests. With proactive service operations, mills can achieve significant long-term cost savings and minimize the consumption of raw materials, and energy.
For this, it was necessary also for Metsä Board Äänekoski to include proactive quarterly onsite service visits as part of their service agreement to decrease total maintenance and production costs, optimize production quality, and minimize web breaks. An essential part of the Procemex service contract is also to provide regular security updates to the camera system. This is achieved through seamless collaboration with the customer’s ICT organization and their subcontractor.
To ensure the service agreement meets every mill’s needs, the content of the Procemex service agreement is always customized. In addition to onsite service visits, Metsä Board Äänekoski’s Service agreement also included 24/7 remote support, quarterly data security updates, and a stock of spare parts for critical elements. “We took the service agreement from Procemex to ensure reliable running and system performance for the years to come. To have our operators make all the service operations for the Web Inspection System would require resources that we currently do not have. To have Procemex specialists take care of the system is far more efficient, and with the current resources, it is a must. Overall, Procemex’s service and support have been working extremely well, and we have found the 24/7 remote support very useful. A solution to service requests and helping advice have been given rapidly, whenever needed,” Paavo Hirvonen sums up.
System virtualization -Easy Integration into existing ICT
Integration into existing ICT was important for Metsä Board Äänekoski. They were very happy that Procemex’s Web Inspection and Monitoring System could be seamlessly integrated with the existing ICT infrastructure. This made the transition smooth, and as Hirvonen states, the system has been easy to use. The virtualization of the system has brought many valuable advantages. As the needs of ICT and systems expand and evolve, the virtualized environment offers scalability and flexibility. An additional advantage lies in the absence of any black boxes within the setup, which would otherwise restrict the mill’s access to it. In contrast, the entirety of the system remains under the customer’s control, ensuring complete ownership and management.
Metsä Board Äänekoski’s decision to choose Procemex is a milestone in pursuing end product quality excellence. Just like in any other project, some challenges were encountered in this project as well. Nevertheless, these challenges were overcome through fluent cooperation and a shared understanding. Procemex’s dedication to innovation, exceptional team, and unwavering commitment to service have enhanced Metsä Board Äänekoski’s defect detection and root cause analysis capabilities and fostered a thriving partnership. With Procemex by their side, Metsä Board Äänekoski is confidently charting a course toward a future defined by excellence and new innovations within the field of AI-enhanced Web Inspection and Web Monitoring.
More Success Stories
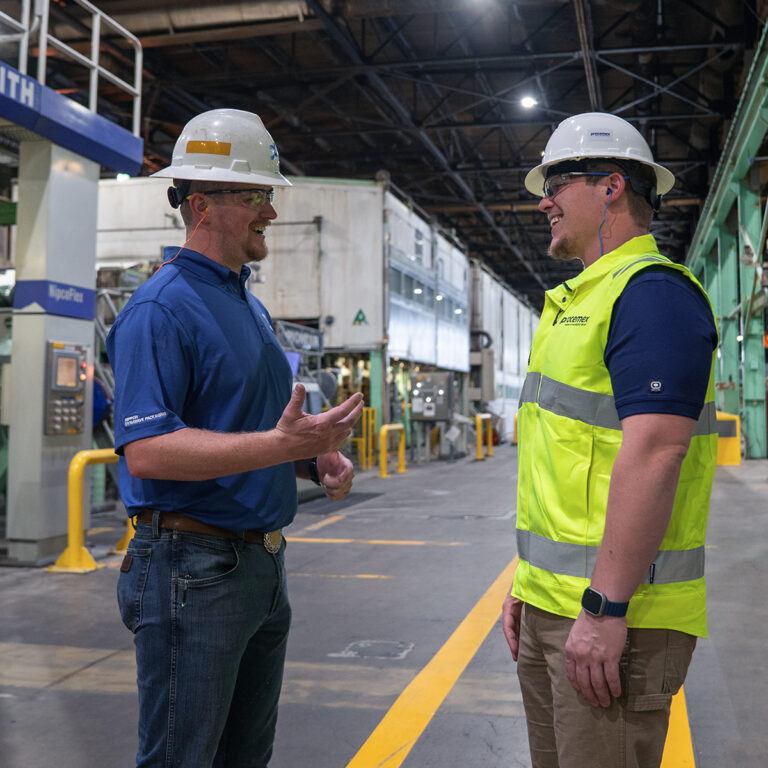
Nippon Dynawave Packaging: Superior Product Quality and Increased Uptime with Procemex Web Monitoring and Web Inspection System
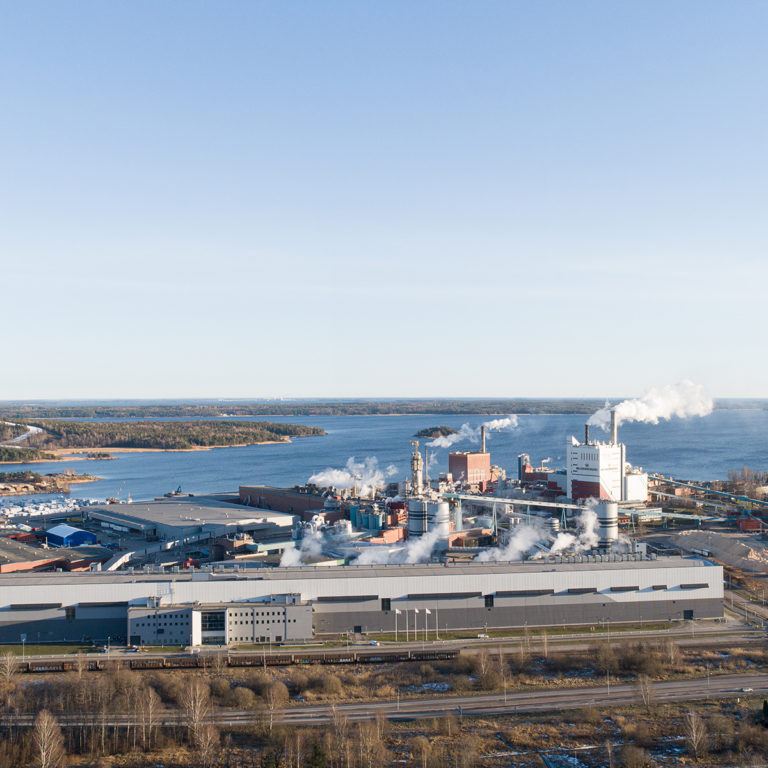
BillerudKorsnäs Gruvön Mill: “We Are Really Happy to Run Procemex OnePlatform System”
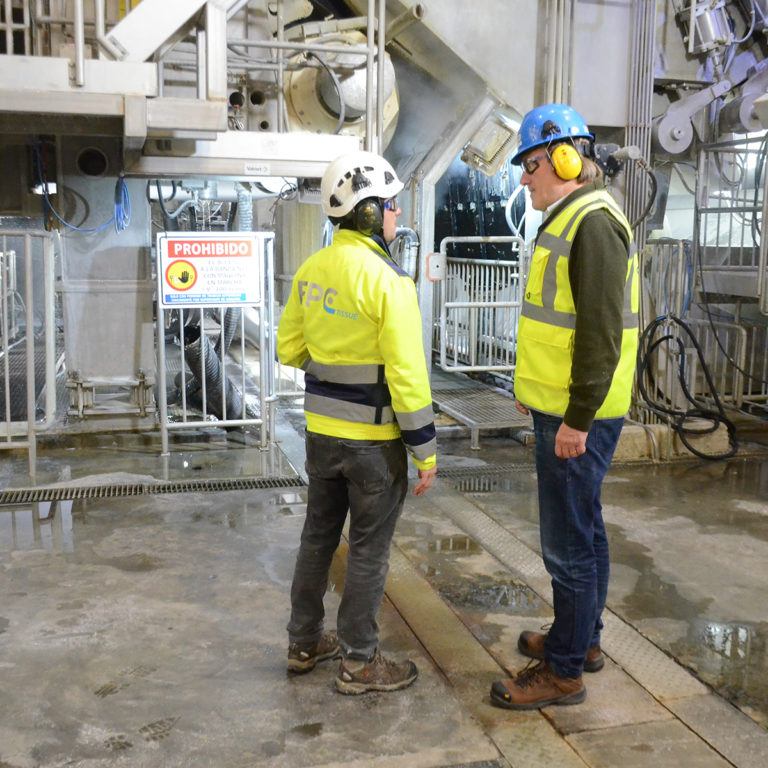
FPC Tissue in Chile Achieves Great Results with Procemex
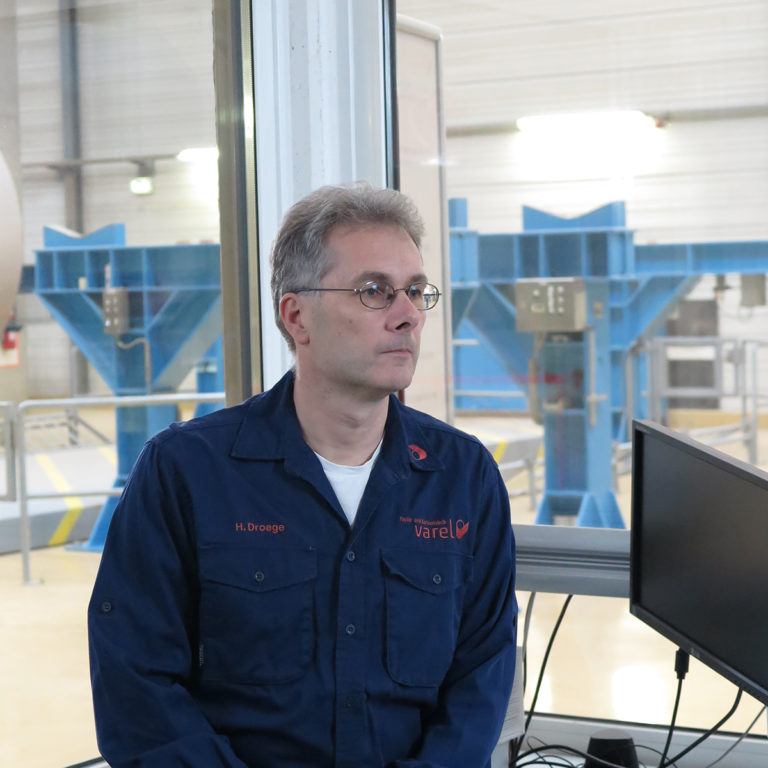