
Barcelona Cartonboard Invested in Integrated Web Inspection System
In 2015, Stora Enso signed an agreement with German private equity company Quantum Capital Partners (QCP) to divest its Barcelona white lined chipboard (WLC) mill. QCP started investments in the mill and the mill launched a two-year investment plan to increase quality and productivity, the total plan being over 15 million euros. The investment plan included eg. a new coater, top former and a new shoe press, to name a few.
This year, Barcelona Cartonboard commissioned Procemex Web Inspection System with high angle reflection inspection on top and bottom sides for their board machine. This new equipment strengthens mill’s capacity to deliver high-quality board. Mr. José Antonio Campo, Technical Director of Barcelona Carton: “At the same time with other investments we wanted to install Procemex Web Inspection System because we wanted to ensure our board quality.”
Quality First
“Our main target is to improve mill’s regularity, since our printer customers have faced problems with blankets or other parts of the machine, and we want to reduce the amount of compensations. With Procemex system we are able to improve our quality, and not just waiting for feedback from customers,” continues Mr. Campo.
Fast Investment Decision
The investment plan was carried out very quickly, because the mill wanted to achieve fast results. “The bidding process was short, but Procemex responded in time, decision was made also right away and Procemex could meet our demands for fast delivery. We wanted to have Procemex installation at the same time as we did the shoe press installation, and it was fine with Procemex,” tells Mr. Alfonso Bello, Production Manager. “The system was calibrated and ready to work at the same time as shoe press. It helps us in reducing break times, especially with breaks taking place at former section and also in the winder.”
“Procemex Web Inspection System has helped us in finding new defects as well: Now we can control the whole production along the machine and see different defects and detect the place of, for instance, drops, edge breaks, lubrication grease, etc.” says Mr. Bello.
Improved Defect Inspection and Problem Solving
All the mill’s shifts were trained during the commissioning, but the mill will have also an additional training after the learning phase. “Now that we have learned the system, we want to get the most out of it and detect the defects that most benefit us,” describes Mr. Campo. “The use of the system will be coordinated together with production and quality personnel. Procemex people help us to find just the right places for the cameras.”
“The winder and sheeter section are now a bottleneck for us and there we will need the information out of Procemex system.”
A good impulse for the investment was also the expectations of customers: “We need to improve our performance, since earlier we didn’t see all the defects that we see now. Reducing the claims and costs of the claims are our main target this year,” tells Mr. José Antonio Campo.
“Now we are able to analyze our board on both sides, and detect defects we didn’t realize there are. We are now working with our chemical suppliers to work this problem out, since now we have the evidence on the problem.”
“The important thing is the tracking,” emphasizes Mr. Bello. “Production and quality people are working closely together to improve the quality in total,” says Mr. Campo. “The image quality is very good, I would also like to have low angle reflection added,” says Production Manager Mr. Bello.
Future Plans
“The next step will be to upgrade also our Web Monitoring System to HD cameras and new lights. Procemex Web Monitoring system can be upgraded and integrated easily to our Web Inspection System,” says Mr. José Antonio Campo.
“I think that after this installation of the integrated Web Inspection System, our operators will pay more attention to the cameras, since now it is easy to find the root cause, analysing is easy,” describe Mr. Campo and Mr. Bello together. “Problems are solved quick and easy and actions are taken right away.”
“After solving our bottlenecks, we are to increase our efficiency substantially and decrease waste,” highlights Mr. Campo. “And upgrading our Web Monitoring System and add more cameras.”
More Success Stories
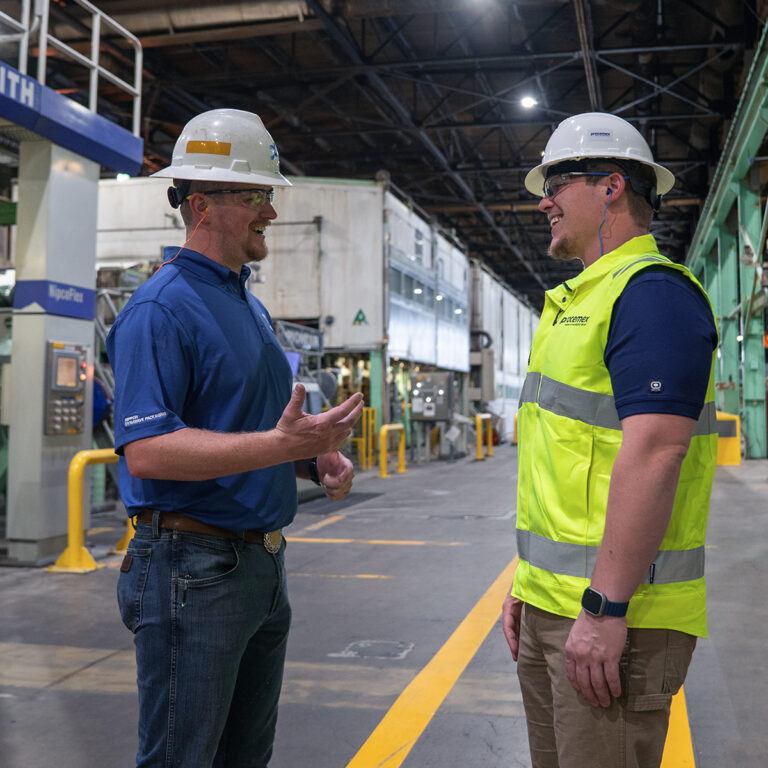
Nippon Dynawave Packaging: Superior Product Quality and Increased Uptime with Procemex Web Monitoring and Web Inspection System
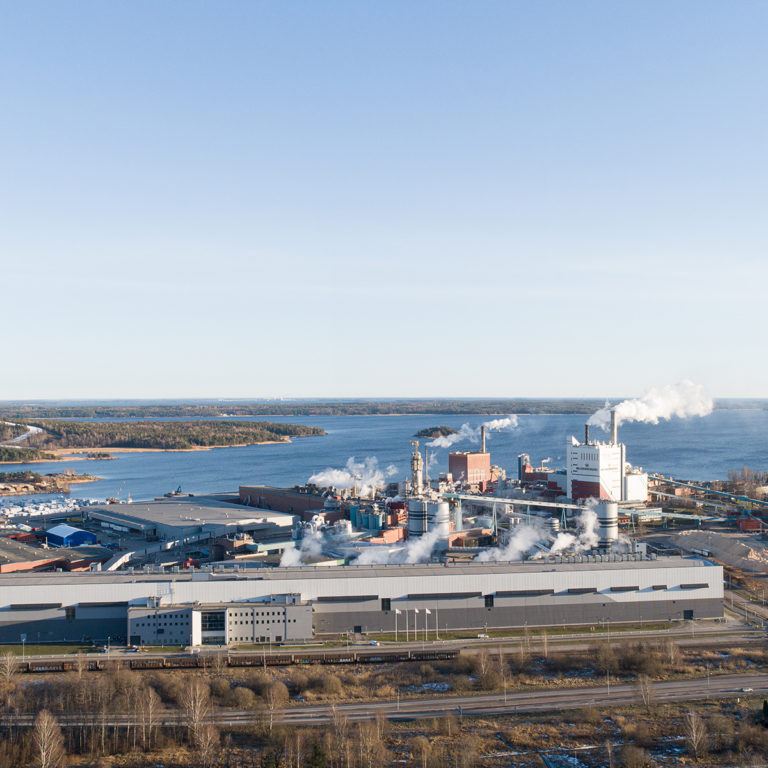
BillerudKorsnäs Gruvön Mill: “We Are Really Happy to Run Procemex OnePlatform System”
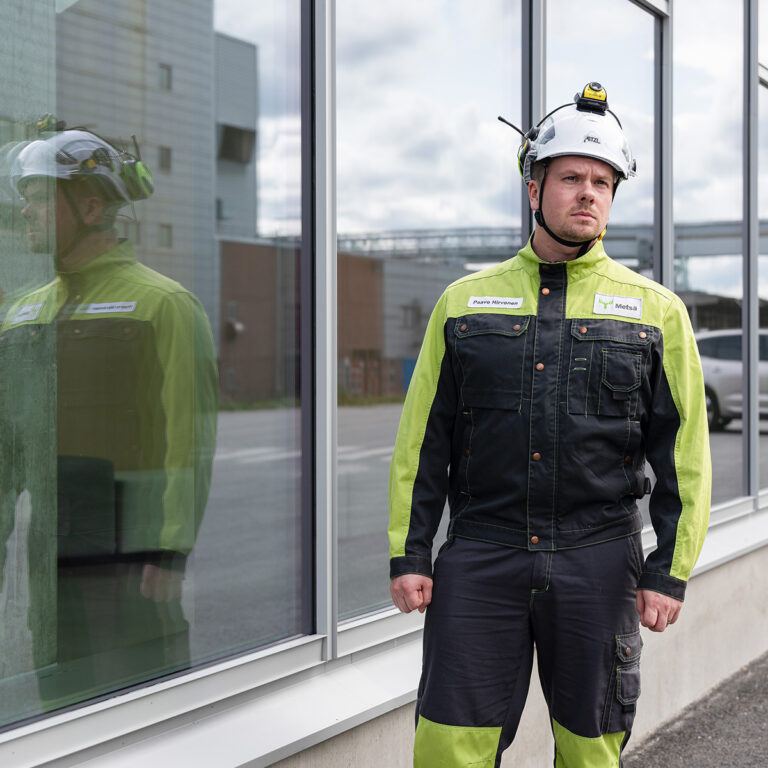
Metsä Board Äänekoski: Higher Customer Satisfaction and Line Efficiency with Procemex Web Monitoring and Inspection System
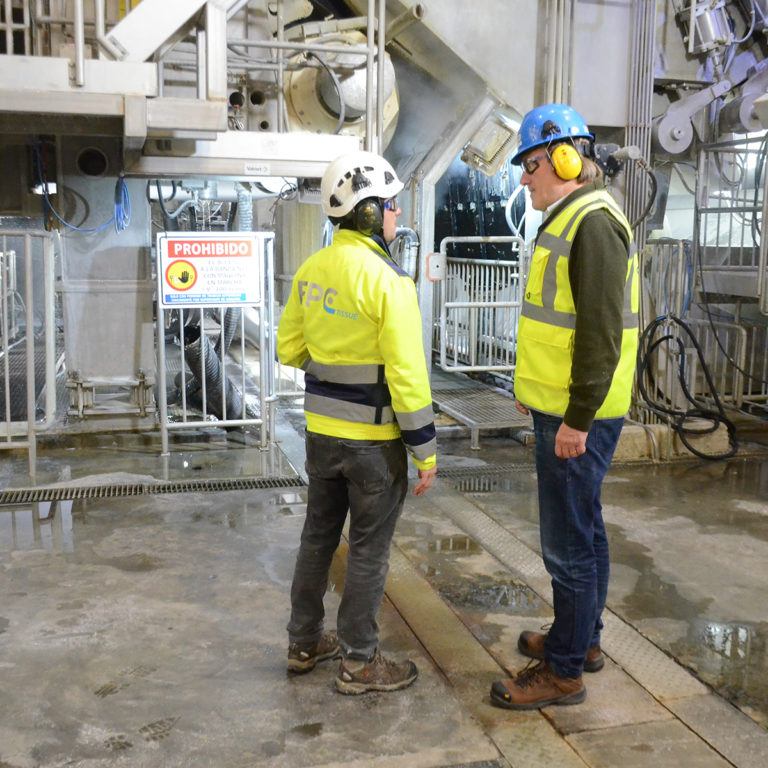